Matériaux et équipements
Réaliser sa planche à voile ou son surf implique de devoir faire le choix de ses matériaux de fabrication, et de s’équiper des outillages nécessaires pour les mettre en œuvre.
La forme, le « shape » (le noyau donc), est constitué d’une mousse plutôt légère, polystyrène (11 à 30 kg/m3) ou polyuréthane (40 kg/m3). Viennent ensuite les peaux extérieures constituées de stratifiés fibre/résine Epoxy (ou polyester), et d’un matériau d’âme pour les structures sandwich.
Ce sont elles qui confèrent au flotteur ses qualités de résistance, de déformation aussi, et de légèreté.
Combien cela coûte t-il ? Quel temps cela prend t-il ?
L' échantillonnage, soit la nature des tissus, leur positionnement, leur grammage, le nombre de couches à mettre en oeuvre, la nature du noyau, des sandwichs, des accessoires, sont à déterminer en fonction du programme et des caractéristiques recherchées.
Les tableaux ci-dessous, donnés à titre indicatif pour une planche de vagues de 75 litres (échantionnages précis disponibles ici), sont basés sur l'expérience, et sur le prix des matériaux chez une liste non exhausive de fournisseurs au mois de janvier 2019. (cliquez sur les images pour les grandir)
Il faut ajouter à tout cela le prix d'achat et de remplacement de l'outillage, tous les ports de livraison pour les fournitures commandées à distance.
Télécharger les tableurs de calcul du prix de revient d'un custom avec une proposition de liens fournisseurs
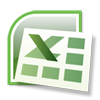
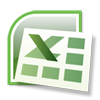
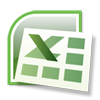
Les fibres
Elles sont nombreuses, fibres de verre, de carbone, de kevlar, ou fibres polyéthylènes (DYNEEMA ou Innegra très en vogue chez les fabricants en 2013, alliées à d'autres fibres), puis plus récemment, fibres de lin. Leurs différents tissages le sont tout autant : taffetas, sergés, satins, unidirectionnels, bi axiaux....)
Lorsque l’on tire sur un matériau, il s’allonge. Si l’on le relâche, le matériau reprend sa forme avec plus ou moins de nervosité (beaucoup pour le carbone, beaucoup moins pour le verre par exemple). Au delà d’un certain allongement (limite élastique), le matériau reste déformé, est dégradé, puis finit par céder.
Un matériau est mécaniquement caractérisé par des valeurs, dont deux sont déterminantes :
- son module d’élasticité E (Méga Pascals MPa, 1MPa équivaut à 100g/mm2), qui caractérise sa rigidité.
- sa résistance à la rupture (en Mpa aussi), qui elle, caractérise l’effort à partir duquel le matériau va se rompre (par exemple, un tissu de verre dont la résistance est de 3000 Mpa, supportera une charge inférieure à 300 kg/mm2 sans céder).
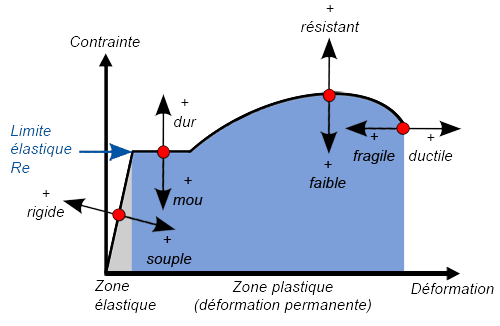
Deux caractéristiques à ne pas confondre donc. Le verre est par exemple moins rigide que le carbone, mais pas nécessairement moins résistant.
Le type de tissage a enfin son importance, et il convient de placer les fibres dans la direction dans laquelle elles "travaillent" le mieux, de considérer la déformabilité du tissu, et son absorption de résine.
Remarque : Les passages « dessus / dessous » des fibres les unes par rapport aux autres dans un tissage étant générateurs de contraintes mécaniques, et d’ondulations du tissu, l’idéal serait de travailler avec des nappes de tissu unidirectionnelles placées judicieusement (les tissus bi axiaux par exemple, superposition de deux nappes d’unidirectionnel placées à 45°).
Les tissages
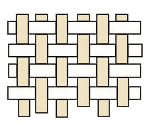
(Plain Weave)
Se déforme peu
Fortes Ondulations
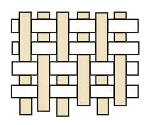
(Twill)
Déformation moyenne
Ondulations moyennes
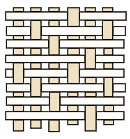
Se déforme bien
Faible ondulations
A titre indicatif, un comparatif des fibres les plus utilisées (les échelles de prix ne constituent qu’une indication comparative) :
Type de fibre | Densité (*) | Résistance (MPa) | Module E (Mpa) | Echelle de prix (en €/kg) |
---|---|---|---|---|
Verre | 2,5 à 2,6 | 2750 à 3900 | 73 à 87 | 1,5 à 15 |
Carbone | 1,8 à 2 | 2000 à 4000 | 200 à 700 | 45 à 600 |
Kevlar | 1,45 | 3500 à 3900 | 70 à 170 | 30 à 125 |
Polyéthylène | 0,96 | 3000 | 100 | 8 |
(*) La densité de l'eau est 1
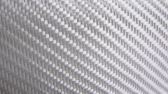

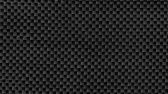
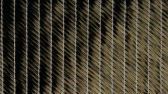
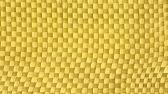
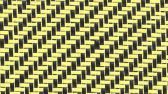
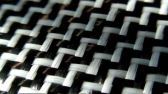
Chaque fibre doit être choisie pour ses qualités, tout en connaissant ses défauts :
Le verre : bonne qualités mécaniques en traction et compression en général, certains verres sont de haute qualité (Verre S ou Verre H), coût abordable pour les verres « standards ».
Carbone : Haute résistance en traction, rigidité, mais peu résistant en compression et aux chocs. Cher.
Kevlar : Très grande résistance à la rupture, grande résistance aux chocs (gilets par balles), peu rigide, mais difficile à stratifier, à couper, presqu’impossible à poncer. Hydrophile.
Fibres polyéthylènes : Une alternative au Kevlar, moins coûteuse, avec le même genre de caractéristiques.
En définitive, le stratifié idéal est une alliance judicieuse de toutes ces fibres, prenant en compte leur poids, leur rigidité, leur résistance, leur orientation, et leur prix.
Attention cependant à une confusion fréquente ! Si la fibre de carbone présente de bonnes qualités (sur un pont par exemple) de résistance à la pression des pieds (effort perpendiculaire à sa fibre qui l'amène donc à travailler en traction!!), c'est grâce à ses qualités en traction ! Sur une carène sur laquelle les fibres se compriment (par flexion du flotteur, voir le schéma ci-dessous), le carbone est donc déconseillé (flotteur de vagues surtout).
Comment se déforme un flotteur ?
Le schéma ci-dessous précise par des flèches les efforts que subit un flotteur lors d’une réception violente : la planche a tendance à subir une flexion dans laquelle la peau externe du pont est plutôt étirée, et celle de la carène comprimée. La fabrication doit être équilibrée, et il n’est pas judicieux de renforcer à outrance un côté de la planche aux dépends de l’autre : pont très renforcé et carène « légère », c’est la carène qui se comprime (pli transversal), et à l’inverse, carène très raide et pont trop léger, c’est lui qui rompt entre le pied de mât et les footstraps de manière transversale.
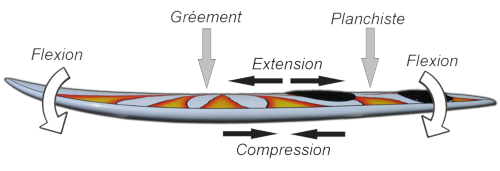
Le sandwich
Une structure sandwich, alternative à une structure monolithique (des stratifiés « empilés » sur un noyau de mousse), nécessite l’usage d’un matériau d’âme, qui, intercalé entre deux stratifiés, leur permet de travailler en traction / compression, et non plus simplement en flexion.
Ce matériau d’âme doit être léger, et résistant en compression, afin de garantir l’espacement entre les stratifiés ou peaux.
Le plus utilisé d’entre tous, dans la majorité des fabrications aujourd’hui, est le PVC. Cette mousse existe en plusieurs densités (50 kg/m3 à 100 kg/m3), en en diverses épaisseurs (3mm à plusieurs centimètres).
Plus une mousse est dense, plus elle est lourde (Compte tenu des épaisseurs utilisées, il y a assez peu de différence entre du 80 kg/m3, et du 100 kg/m3, soit 60 gr de différence par m2 pour du 3mm), mais plus elle est résistante en compression (avantageux pour le pont de la planche en particulier). Le PVC présente en plus l’avantage d’offrir une surface de collage importante, donc d’être moins sujet au délaminage.
Les autres matériaux de sandwich très connus, sont le nid d'abeille, le bois, le spheretex, et plus récemment, le liège.
Ces structures sandwich nécessitent l’utilisation d’un système de mise sous-vide afin d’être correctement plaquées sur le noyau.
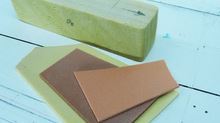
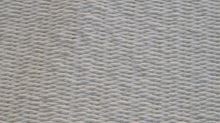
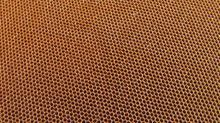
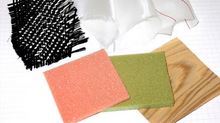
Les résines
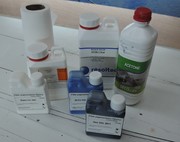
Pour pouvoir travailler sur des mousses polystyrène, il est impératif d’utiliser des résine de type époxy (le polyester fond la mousse polystyrène).
Elles présentent en outre de bien meilleures qualités mécaniques que les résines polyester (seul le milieu très conservateur de Surf persiste à les utiliser encore aujourd’hui prétextant une déformabilité supérieure appréciée des surfeurs), mais s’avère aussi plus exigeante en température, pour polymériser correctement (minimum de 20°C, un étuvage à 60°C étant idéal pour augmenter ses caractéristiques mécaniques)
EPOXY | POLYESTER |
---|---|
Avantages Très bonnes qualités mécaniques Résistant à l'abrasion Faible odeur (Toxique quand même) compatible avec toutes les mousses Inconvénients Ponçage plus difficile Temps de polymérisation important Température requise 20°C minimum Moins translucide, moins "fluide" Prix élevé |
Avantages Très translucide, bonne imprégnation Polymérisation rapide Température requise plus basse (15°C) Ponçage aisé, facile à lustrer Economique Inconvénients Qualités mécaniques médiocres Tendre, sensible aux rayures Odeur forte Incompatible avec les mousses polystyrènes |
Remarque :
L’étuvage des résines Epoxy « repousse » également la température à laquelle le stratifié pourra résister par la suite (le "Tg") (par exemple, une planche non étuvée, placée en plein soleil, vis de décompression fermée, risque de se délaminer, parce que la résine redevient souple, et que l’air contenu dans le polystyrène se dilate, donc pousse…)
Environnement de travail et outillage
Pour travailler dans de bonnes conditions, un outillage et un environnement adaptés sont nécessaires.
Bien se protéger
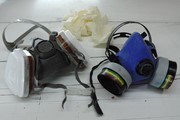
Pour découper le polystyrène et shaper (façonner)
- Système de fil chaud
- Outils de mesure
- Scie égoïne
- Scie sauteuse
- Rabot électrique
- Surform (râpe à main)
- Cales à poncer, rigides et souples, sandscreen
- Règle alu 3m pour vérifier la ligne de rocker
- « Bumper » (support de planche)
- Eclairage « rasant » adapté
- Compresseur (soufflette / peinture)
Pour stratifier :
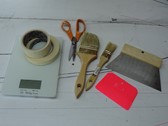
- Pinceaux
- Raclette crantée et squeegee (raclette souple)
- Scotch de masquage
- ciseaux
- Balance (proportions résine / durcisseur)
- Pièce chauffée, voire étuve
Pour mettre sous vide :
- bâche à vide (bâche tubulaire)
- Pompe à vide et système de pompage
- Drain, films séparateurs perforés ou non (consommables)
Pour poncer et défoncer :
- Ponceuse excentrique
- Meuleuse d’angle équipée d’un abrasif
- Défonceuse (pose des accessoires)
- Défonceuse, meuleuse et excentrique
Enfin, un local "dédié", chauffé, ventilé et équipé d'un bon éclairage, permettra de travailler confortablement.
Les outils utilisés pour la fabrication d’une planche peuvent être dangereux, de même que tous les produits chimiques. Les protections telles que masques (solvants, poussières, peintures) et gants sont indispensables.