Qu’est-ce qu’une structure « Sandwich »
Elle s’est petit-à-petit imposée, face à la classique structure Monolithique qui consiste à recouvrir un noyau de mousse polystyrène ou polyuréthane, de couches de stratifiés. La solidité de la structure étant obtenu par un choix judicieux des bonnes fibres, alliées aux résines adaptées, et du bon nombre de couches. Plus ces couches sont nombreuses, plus la structure est résistante, mais lourde.
Dans le milieu du Windsurf, la nécessité d’encaisser des efforts considérables, tout en conservant des structures légères, a naturellement conduit à une alternative : le sandwich. Même si elle tend à s’imposer également dans le milieu beaucoup plus « conservateur» du surf, certains persistent à lui reprocher sa rigidité importante, et son « manque » de toucher d’eau.
Pourtant, en plaçant les fibres dans des directions adaptées, et en utilisant des âmes de sandwich souples (comme le liège), on arrive aujourd’hui à régler le problème en question.
Utiliser une structure sandwich consiste donc à intercaler entre deux stratifiés, un matériau « neutre » (dit matériau d'âme), dont les qualités mécaniques ne sont pas déterminantes (à part en compression, afin de maintenir l’espace entre les stratifiés), mais qui a pour effet, en éloignant ces deux stratifiés, de créer un « effet de poutre », et de rigidifier considérablement le complexe : les stratifiés, au lieu de travail en flexion, sont soumis à des contraintes de traction et compression.
Plus l’épaisseur du sandwich est élevée, plus sa rigidité est importante. Il s'agit exactement du même principe que celui qui permet à du carton ondulé d'être à la fois rigide, résistant et léger.
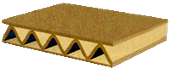
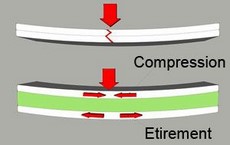
Les stratifiés sont en général réalisés à partir de tissus de verre, carbone ou kevlar, et de résines époxy ( les résines de type polyester étant incompatibles avec les mousses polystyrènes, et de mauvaises qualités mécaniques).
Les matériaux de sandwich, pour ne citer que les plus utilisés, sont de type mousse PVC, usuellement utilisée en 3 à 8 mm dans des densités variant de 50 à 100 kg/m3 ), spheretex en 1,2 ou 3 mm (résistant, mais plutôt lourd dans les épaisseurs intéressantes si l’on ne maîtrise pas sa saturation), Nid d’abeille en 3 ou 5 mm (mise en œuvre délicate, coût élevé, grande rigidité, peu adapté aux flotteurs de vague), ou encore de type BOIS ( matériau fibreux possédant de bonnes qualités mécaniques suivant son propre fil) en 6/10e d’épaisseur.
Voir catégorie : Matériaux et équipements
Chaque matériau de sandwich présente ses caractéristiques mécaniques et physiques (résistance à la compression et densité en particulier), son coût, et sa méthode de mise en œuvre.
En fonction du type de programme, de la rigidité et du poids désirés, on retiendra tel ou tel type de sandwich, et tel stratifié.
La principale difficulté dans la réalisation d’une structure sandwich, réside dans le fait de plaquer ces matériaux (en particulier le PVC, l’un des meilleurs compromis, qui cependant doit être thermoformé au préalable) sur les formes complexes de pont ou de rails d’une planche. Pour cette raison, les plaques utilisées pour le pont seront d’épaisseur 3mm, bien plus faciles à préformer, et mécaniquement très suffisantes.
Enfin, l’utilisation de mousses de densité élevée (100 kg/m3), garantira au flotteur une excellente tenue en compression (plutôt pour le pont).
La réalisation d’un sandwich de carène reste assez sommaire, compte tenu de la forme suffisamment plane qu'elle offre comme support. Pour cette raison, il est recommandé d’utiliser de la mousse de 5 mm d’épaisseur, qui offrira un sandwich plus résistant.
Leur mise en œuvre nécessite quoiqu’il en soit l’utilisation d’un système de pompage à vide (voir page vidéos).
Pour le collage des matériaux d’âme, on utilise de la résine chargée (la silice permet d’obtenir un gel époxy qui ne pénètre pas dans les supports), ou des colles de structure, lorsque la surface de collage est réduite (nid d’abeille).
En quelques croquis, voici les étapes sucessives de shape et mise en place des sandwichs de pont et carène